Those responsible for buying emergency-response products such as instruments and devices can be easily overwhelmed by the huge number of choices available. For that reason, it is important that purchasing departments (and individual buyers) develop and implement a prioritized purchasing system – one that places proven reliability as a principal criterion in purchasing decisions.
There are two essential factors that are (or should be) used to determine the reliability of a product. The first is whether an acceptable volume of verifiable independent testing data has been provided by the manufacturer that certifies that the product being considered for purchase is both technically and scientifically sound. The second essential factor is the manufacturer-provided data on relevant consumer experience, performance testing, and training results – all of which, combined, should be a reasonable guarantee of user success. The potential buyer should keep in mind, though, that a testing result can be flawed just as much by scientific/technological errors as by user error. In short, the instrument or device purchased might well be useless without the double layer of proven reliability.
It also is important to remember that, although the Department of Homeland Security (DHS) publishes acceptable performance standards (on the DHS webpage) for most if not all emergency medical services (EMS) instruments and equipment, it is still the responsibility of the EMS buyer to collect enough information, and then analyze it sufficiently, both to provide better customer service and to spend government and/or company funds wisely. Some product information is provided upfront by manufacturers on the inserts that they almost always include with the product, and considerably more information usually can and will be provided by the same manufacturers if the buyer requests it. Product information also is available from many well known EMS resources – e.g., the Responder Knowledge Base – and through general EMS networking and communications.
Stress-Test Data May Take Greater Diligence
With regard to an instrument’s performance under stress, it is particularly important for the EMS buyer to: (1) ask the manufacturer for product performance data in stress areas of interest (weather, rough handling, etc.); (2) also ask about any known product limitations that are already known by the manufacturer; and (3) talk to other responders who have used the equipment in stressful or “rugged” situations. Environmental testing is usually a very expensive proposition for a manufacturer, so the buyer may have to ask for independently conducted environmental testing data, with the specific testing parameters included, before making a purchase decision. It would be up to the manufacturer, of course, to decide if such testing would have sufficient commercial value.
Voluntary consensus performance standards usually are developed through balanced inputs from stakeholders who contribute the scientific knowledge, technological capability, and experience required to protect the public and/or to improve its standard of living. If the EMS buyer is not sure if a voluntary consensus performance standard is available for a particular product, that question could be answered by a telephone call or email to a member of the staff of the American National Standards Institute (ANSI) – preferably someone assigned to the ANSI Homeland Security Panel. Every business wants to be able to claim that its products conform to the ANSI standards, so the ANSI list is a good one for buyers to refer to when communicating with manufacturers about the standards their instruments and devices are measured against.
The EMS buyer may not always be able to find a published performance standard for the product being considered for purchase. For that reason it is important to keep in mind that a manufacturer’s use of a certain performance standard is voluntary, which means that a manufacturer has the option to develop and/or use alternative standards (and also can either modify established standards or use them only in part) – if the alternative standards meet the same essential principles used in setting the established standards. In these cases, the purchaser would have to compare the manufacturer’s testing data with the data accumulated on products known to follow established standards.
But What If …?
If the purchaser of EMS instruments and devices is unable to find a published performance standard for the product, that does not mean that an acceptable standard does not exist and/or that acceptable performance criteria have not been established. Indeed, the homeland security community endeavors not only: (a) to stay receptive to extant standards, and to the new standards being developed almost every day (on an international scale); but also (b) to stay receptive to the advent of new technologies. The bottom line here is that, no matter what the source of a manufacturer’s performance standard, it would be up to the manufacturer to supply the purchaser with the documentation needed to prove the reliability of the product and ensure that it conforms to a desired and acceptable standard.
In short, the buyers of EMS instruments and devices should always be very careful in making their decisions. But in today’s market they usually do not have to be overly concerned, either, about most of the EMS products now offered. Acceptable and verifiable performance standards are almost always available – as well as cogent advice and guidance from ANSI, standards developers, and the Department of Homeland Security itself. In the final analysis, when the buyer has any reasonable question regarding a new standard, it is up to the manufacturer to produce data for the buyer that shows conformance with products that are already meeting published standards and/or that meet the essential principles of previously established standards.
For additional information on performance standards: (a) email or call a member of the ANSI staff assigned to that organization’s Homeland Security Council (e.g., mdeane@ansi.org/1-212:642-4992 or jcarl@ansi.org/1-212:642-4903); or (b) consult the Standards and Guidelines sections of the DHS webpage; or (c) review the standard list.
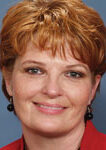
Diana Hopkins
Diana Hopkins is the creator of the consulting firm “Solutions for Standards.” She is a 12-year veteran of AOAC INTERNATIONAL and former senior director of AOAC Standards Development. Most of her work since the 2001 terrorist attacks has focused on standards development in the fields of homeland security and emergency management. In addition to being an advocate of ethics and quality in standards development, Hopkins is also a certified first responder and a recognized expert in technical administration, governance, and process development and improvement.
- Diana Hopkinshttps://domesticpreparedness.com/author/diana-hopkins
- Diana Hopkinshttps://domesticpreparedness.com/author/diana-hopkins
- Diana Hopkinshttps://domesticpreparedness.com/author/diana-hopkins
- Diana Hopkinshttps://domesticpreparedness.com/author/diana-hopkins